What determines when a sample is taken. I'm ordering all the fruit from Bruce, so when the valve is opened to a new lift point, does the operator click a button on the screen, or better yet, is there a foot pedal that can be depressed to take the sample?
I'm trying to work out how to interface another item with the system.
Basically I'm builidng an automatic valve opener and I've been trying to work out the best way to automate everything. If it can work with a foot switch we're laughing.
The valve opener is a bit over the top, however I'll be mainly working on one engine, a Nissan SR20VE. I'll also make a secong one that is a universal one that will fit a rail like Bruce's universal rail.
what determines when a sample is taken
-
- Posts: 46
- Joined: Wed Dec 23, 2015 6:49 pm
what determines when a sample is taken
You do not have the required permissions to view the files attached to this post.
-
- Site Admin
- Posts: 1852
- Joined: Fri Jan 08, 2010 3:35 pm
- Location: Pennsylvania
- Contact:
Re: what determines when a sample is taken
On the PTS DM you have a running average so you can take the sample at any time
Bruce
Who . . . me? I stayed at a Holiday in Express . . .
Who . . . me? I stayed at a Holiday in Express . . .
-
- Posts: 46
- Joined: Wed Dec 23, 2015 6:49 pm
Re: what determines when a sample is taken
Ok.
So the operator does something to take the sample such as uses a mouse or a foot pedal?
So the operator does something to take the sample such as uses a mouse or a foot pedal?
-
- Posts: 1338
- Joined: Fri Jan 08, 2010 10:36 pm
- Location: Maryland
Re: what determines when a sample is taken
Once set up for a test by inputting the test point increment you click the open file button then it turns into the read data button each time you click it will increment to the next test point.
-
- Posts: 1438
- Joined: Wed Mar 03, 2010 3:40 pm
- Location: Melbourne, Australia
Re: what determines when a sample is taken
Yes, basically once the valve(s) have been moved to the next lift increment, it takes some finite time for the bench motors to adjust themselves back to to the exact set test pressure, because the flow will have obviously changed.tafeteacher wrote:Ok.
So the operator does something to take the sample such as uses a mouse or a foot pedal?
The operator then uses some judgement as to when the test pressure is again stable, and the new measurement values recorded the way Rick says.
Its then up to the operator to again move the valves to the next lift increment either manually or by your magic gadget.
The automatic valve lifter could be stepped by pushing a button (or a foot switch) to do that automatically. There may be some merit in having a rotary switch. It would then be possible to step in either direction, go back, or jump over certain lift values.
The valve lift machine can then be an entirely separate entity without any connections to either the automatic pressure controller or the flow bench monitoring electronics and software. It could be added as a new feature to ANY flow bench without requiring any interfacing, and avoid all the problems that would probably entail.
One time proven engineering philosophy to bear in mind.
With critical equipment such as life support, mission critical military, aerospace, or the nuclear industry, we need to be absolutely certain that what we wish to see happen actually does happen.
Any fault, failure, or inaccuracy must become immediately apparent to the operator. We do that by keeping what creates the desired action, in this case commands a new valve lift, completely separate from the monitoring system that measures and displays actual measured valve lift. If you set 0.200 lift and the measurement readout says its 0.195 you know for sure either the actuator or the measuring device has now developed a problem. Something has changed and you can then investigate.
In this case, a pair of dial indicators would seem to be the simplest and most appropriate, but something electronic could also serve the same purpose.
If both continue to agree precisely, you can have absolute confidence that everything is fine.
Also known as the infamous "Warpspeed" on some other Forums.
-
- Posts: 46
- Joined: Wed Dec 23, 2015 6:49 pm
Re: what determines when a sample is taken
Thanks Tony
So, from what I can see the DM needs a click or something to tell it to take the sample. We'll work that out.
We won't be using a rotary switch. It will only really have an on/off switch. The Valve lifter will wifi to a phone or tablet (or PC) and the controls will be symbols on the touch screen or computer screen. It will have and up and down button, set home button, speed button or slider, take sample button and a configuration section for setting required lift, number of lifts and speed of lifts. I guess we'll have to have a metric/imperial toggle as well.
Initially we are going to have it lift to a distance, hold for predetermined amount of time, then make the DM take a sample (will work that out when it arrives), then lift again to the next lift station, hold for predetermined amount of time, then make the DM take a sample. repeat.
Imagine the interface is a bit like a CNC controller.
I think I'll do a single valve universal unit before I make the dual valve jobbie, just to speed up development.
So, from what I can see the DM needs a click or something to tell it to take the sample. We'll work that out.
We won't be using a rotary switch. It will only really have an on/off switch. The Valve lifter will wifi to a phone or tablet (or PC) and the controls will be symbols on the touch screen or computer screen. It will have and up and down button, set home button, speed button or slider, take sample button and a configuration section for setting required lift, number of lifts and speed of lifts. I guess we'll have to have a metric/imperial toggle as well.
Initially we are going to have it lift to a distance, hold for predetermined amount of time, then make the DM take a sample (will work that out when it arrives), then lift again to the next lift station, hold for predetermined amount of time, then make the DM take a sample. repeat.
Imagine the interface is a bit like a CNC controller.
I think I'll do a single valve universal unit before I make the dual valve jobbie, just to speed up development.
-
- Posts: 1338
- Joined: Fri Jan 08, 2010 10:36 pm
- Location: Maryland
Re: what determines when a sample is taken
The DM has the ability to read a digital input (D1 input) from a switch for sampling once the process is initiated, at the current time we are struggling with the new AD boards sensitivity to noise causing the sampling to create issues in functionality so it is turned off. The process of using a stepper with rotary encoder along with motor control via PWM can all be handled in an Arduino performing a sweep test and outputting the data to a CSV file. This system has been prototype'd but the main issue i currently am dealing with is the attempt to get GOOD synchronous serial communication between the Arduino and the PC via VB.
Rick
Rick
-
- Site Admin
- Posts: 1852
- Joined: Fri Jan 08, 2010 3:35 pm
- Location: Pennsylvania
- Contact:
Re: what determines when a sample is taken
If I can get the Arduino DM to work in native code (with my excellent coding skills1960FL wrote: This system has been prototype'd but the main issue i currently am dealing with is the attempt to get GOOD synchronous serial communication between the Arduino and the PC via VB.
Rick



I'm sure you can do it . . . I have faith in you figuring it out!



I think the next step in the DM advancement will be a major upgrade to the DIY Flowbench world!
Bruce
Who . . . me? I stayed at a Holiday in Express . . .
Who . . . me? I stayed at a Holiday in Express . . .
-
- Site Admin
- Posts: 1852
- Joined: Fri Jan 08, 2010 3:35 pm
- Location: Pennsylvania
- Contact:
Re: what determines when a sample is taken
The current DM (12bit model) as Rick stated has an issue with the digital switch (D1) being to sensitive so the units I am sending out have the wires but they are not connected inside the box. Once that issue gets resolved I will let everyone know they can connect those wires back up.
The Automatic Motor Control (PID) is in no way connected to the DM, it is a stand alone unit and reads it's own pressures, it was designed this way so it could be used on any flowbench application.
If you have a 194, 145, or 148 model this is not an issue and D1 can be used with a momentary switch connected to D1
The Automatic Motor Control (PID) is in no way connected to the DM, it is a stand alone unit and reads it's own pressures, it was designed this way so it could be used on any flowbench application.
If you have a 194, 145, or 148 model this is not an issue and D1 can be used with a momentary switch connected to D1
Bruce
Who . . . me? I stayed at a Holiday in Express . . .
Who . . . me? I stayed at a Holiday in Express . . .
-
- Posts: 1438
- Joined: Wed Mar 03, 2010 3:40 pm
- Location: Melbourne, Australia
Re: what determines when a sample is taken
I think it would be a good idea to keep the digital manometer quite electrically separate from anything else if possible, for electrical noise reasons.
If the serial data is being corrupted, you could try looping the cable between the DM and the host computer several times around a large high permeability ferrite toroid.
The material is important. Most toroids you will come across are more likely to be powdered iron, which is usually coated with a coloured coating. Powdered iron will not work in this application. Inverter grade ferrite may work, but is less than ideal bit is better than nothing.
If this idea looks promising and solves the noise problem we can try and source the right stuff
Ferrite will always be a dull grey/black in appearance as in the picture below. If its yellow, or red or brown or some other colour its definitely not ferrite. The light has reflected brightly off ferrite in the picture below, it looks almost silver, but it should look more a dull dark almost mat black in more normal light.
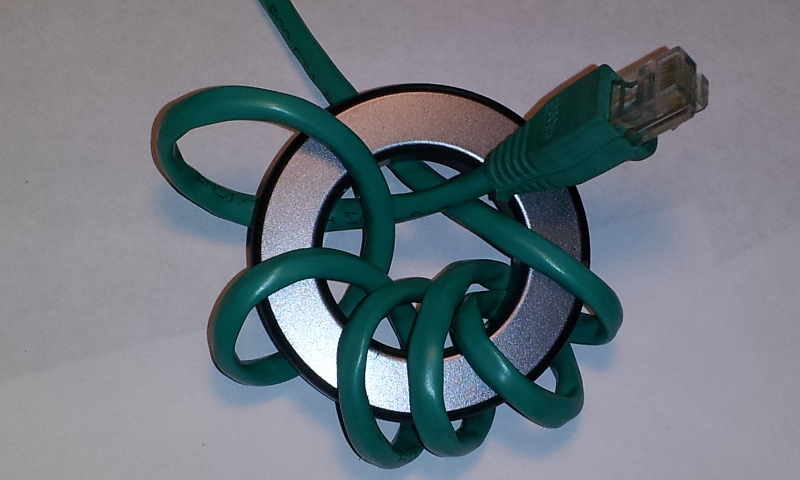
This will be far more effective than the usual clamp around type of ferrite sleeve you will see everywhere.
Nobody uses the toroid method because its big and ugly. The hole obviously needs to be large enough for the connector to pass through, and the wire cannot be wound around neatly. But its much more effective.

If the serial data is being corrupted, you could try looping the cable between the DM and the host computer several times around a large high permeability ferrite toroid.
The material is important. Most toroids you will come across are more likely to be powdered iron, which is usually coated with a coloured coating. Powdered iron will not work in this application. Inverter grade ferrite may work, but is less than ideal bit is better than nothing.
If this idea looks promising and solves the noise problem we can try and source the right stuff
Ferrite will always be a dull grey/black in appearance as in the picture below. If its yellow, or red or brown or some other colour its definitely not ferrite. The light has reflected brightly off ferrite in the picture below, it looks almost silver, but it should look more a dull dark almost mat black in more normal light.
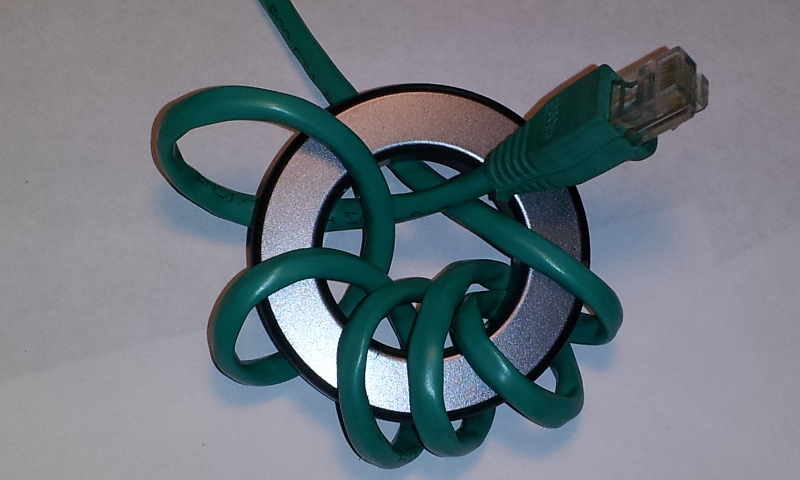
This will be far more effective than the usual clamp around type of ferrite sleeve you will see everywhere.
Nobody uses the toroid method because its big and ugly. The hole obviously needs to be large enough for the connector to pass through, and the wire cannot be wound around neatly. But its much more effective.
Also known as the infamous "Warpspeed" on some other Forums.